About our quilts
Natural Quilts produce 'Jaipuri quilts and quillows', which are handmade using environmentally friendly hand block printing and natural dyes, meaning they are free from harmful chemicals or processes. These quilts are different from Quilts made in Western Countries. Quilts in Europe and America usually have intricate machine stitching. 'Jaipuri' quilts are loosely hand stitched all over to give a softer, more fluffy 'finish'. Sometimes, the hand stitching is knotted, but the threads can come loose. They can be cut off and it will not affect the performance or durability of the quilt.
Our company promotes traditional crafts made ethically from natural materials. The quilts using vegetable dyes fade naturally over time due to the absence of chemicals to set the dyes. This combined with hand block printing makes each quilt unique. We are very proud to have designed the 100% cotton 'Jaipur quillows' and to have them made by people in their homes, not in a factory. They are not mass-produced and there are no middlemen; the wooden blocks are designed by us (and sometimes by other artists). We spend days with our team of printers block printing together and deciding which colours look best.
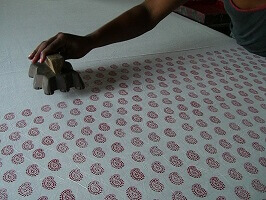
Background
Natural quilts are a speciality of Jaipur in Rajasthan, the desert region of north-west India. Nobody quite knows when and how this mini marvel came into being. Why did Rajasthan alone become the home of this unique form of winter covering when quilts were common all over? Certain factors seem to have played a part, the inhospitable desert terrain, the bitter winter and the age-old Rajasthani penchant for being constantly on the move. Sundown in winter always sent the temperatures plummeting among the dunes. For those who stayed home, there was warmth enough but to many a Rajasthani male, home was none other than the dunes themselves with only the sky for cover. Princes and chieftains on the warpath, soldiers in the saddle, banjaras (gypsies), bhopas (itinerant bards), shepherds, traders, camel caravans rolling along the featureless sands on private business- they all needed something to keep the chill out without adding significantly to their saddle bags. And some unsung genius found the perfect answer in the Jaipuri quilt.
The process
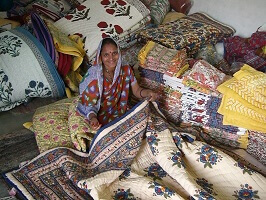
What is unique about the tradition of hand block printing is that it is practised without the aid of mechanization or computerization. It is this defiant indifference to mechanization that gives block printing the aura of a pure craft form and makes block printed textiles so special. The main tools of the printer are blocks of teak wood with handles, one for each colour, carved to allow the design to stand up in relief. The block carving process needs a high degree of craftsmanship especially for the making of the outline block. An accurate freehand drawing of the design on tracing paper is transferred to the planed wood and then chiselled to the depth of a third of an inch. Each colour needs a different block. New blocks are soaked in oil for a few days to soften the grains in the timber.
The fabric to be printed is stretched over the printing table and fastened with small pins. When the block is applied, it is slammed hard on the fabric where the pattern appears in reverse. A point on the block serves as a guide for the repeat impression, so that the whole effect is continuous and not disjointed. The outline printer has to be very skilled because he leads the process. If it is a multiple colour design, the second printer uses his block to fill in the colour and so on. It is interesting to estimate the number of blocks used in the printing of a quilt. Each colour will have its own block so will each component of the design. A border, in addition to the main design, may use several sets of blocks, depending on its complexity, size and sequence.
After printing, the fabric is sometimes steamed and then dried out in the hot Rajasthan sun which helps to set the natural dyes without using chemicals.
Jaipuri quilts are unique in using light, fluffy pure cotton as a filling. The skilled craftsmen take freshly harvested cotton and make it light and fluffy resembling soft clouds by a process called carding. The lighter the quilt, the more evenly it is filled and you will find it warmer and more comfortable. The actual hand quilting to hold the filling in place is done by women in their own homes. A double quilt takes a woman around four hours to complete.
Natural Dyes
Many of our fabrics are printed and dyed using Natural Dyes. A variety of colours can be achieved using natural dyes. You can see below how some of these colours are made and that Natural Dyes are affected by many factors including air temperature and humidity. The resulting fabrics vary from one batch of dyeing or printing to the next making each piece unique.
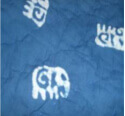
Blue from the Indigo plant
Observe the rich blue achieved from the Indigo plant. The leaves are soaked in water for several hours until compounds from them collect in the water. The leaves are removed and the water whisked exposing it to the air and forming the indigo residue that is then used for dyeing and printing. This is an environmentally friendly process as the plants require little maintenance and are often used to revitalize soil between crops. The soaked leaves are also sold on as an organic fertilizer.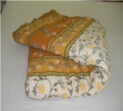
Yellow from Turmeric and Pomegranate
Yellow dye can be made by boiling pomegranate shells for 48 hours; the liquid is strained and mixed with ground Turmeric in a copper pot. The Hindi word for Turmeric is Haldi, and is often used as a food spice. Turmeric provides a strong dye either with or without the Pomegranate; it is often used in conjunction with other dyes such as Indigo to produce a green, or with Madder root to achieve a rust/orange colour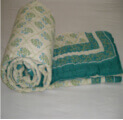
Green from Turmeric, Pomegranate and Indigo
Turmeric and Pomegranate are used to create yellow dyes which are often used over the top of an Indigo dyed or printed fabric resulting in an overall green effect. The yellow dyes are light sensitive and over time your green fabric will become more and more blue (indigo is far more stable) with successive washing and wearing.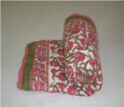
Red from Alum and Alizarin
Alizarin commonly comes from the dried root of the madder plant (though other roots are also used). The Alum (a metal compound) which acts as a mordant is first printed onto the fabric as a colourless paste. When this is immersed into a vat of Alizarin, the two compounds react with each other and turn red.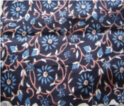
Black from Iron, Sugar and Alum
Rusted Iron (often from old horse shoes) is soaked in a mix of sugar solution (sugar from molasses) and flour made from Tamarind seed. This is left to ferment in the sun for a couple of weeks. The resulting paste produces a rich black, quite different from that made from chemical dyes.Natural versus synthetic
You may think that a quilt with synthetic filling may be better than a naturally filled one, you may prefer the modern to the traditional. But you would probably feel differently if you had the chance to make a proper comparison. User trials conducted by an independent market research company over a two month period showed that, after sleeping under both natural and synthetic quilts, an amazing 75% of users said they preferred the natural quilts.
There are many reasons for this:
- Firstly, naturally filled quilts breathe in a way synthetic quilts cannot. So the moisture lost by your body while you sleep is absorbed overnight, and then gradually lost in the morning when the quilt is aired. When you sleep under a synthetic quilt, there is nowhere for that moisture to go resulting in a sticky feeling.
- Secondly, natural quilts drape better around the lumps and bumps of your body, while synthetics can be rather stiff. Because you can snuggle into it better, a natural quilt will usually feel warmer on a chilly night than a synthetic quilt of the same thickness, even if both are new.
- Thirdly, a natural quilt will almost always be lighter than a synthetic one. Natural fillings bring warmth without weight, for a really comfortable, natural sleep.